When two separate surfaces touch each other such that they become mutually tangent, they
are said to be in contact
In the common physical sense, surfaces that are in contact have these characteristics:
- They do not interpenetrate.
- They can transmit compressive normal forces and tangential friction forces.
- They typically do not transmit tensile normal forces (that is, the surfaces are free to separate and move away from each other).
Target or Contact
In Mechanical, the surfaces on one side of a contact region are referred to as the Contact side, and the surfaces on the other side are referred to as the Target side.
The geometry associated with the Contact side is colored in red , and the geometry associated with the Target side is colored in blue.

Physical contacting bodies do not interpenetrate. Therefore, the program must establish a
relationship between the two surfaces to prevent them from passing through each other
during the course of analysis.
When the program prevents interpenetration, we say that it enforces contact compatibility
Mechanical offers several different contact formulations to enforce compatibility at the
contact interface.
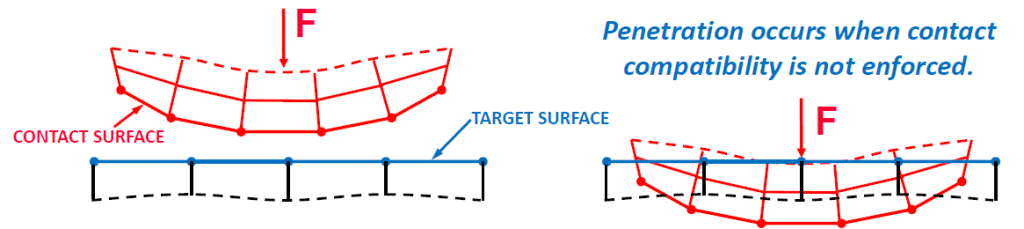
Contact Formulations
Contact Formulations available in ANSYS Mechanical were presented in detail in ANSYS Mechanical Basic Structural Nonlinearities and are summarized here.

Default Formulation is Augmented Lagrange for all flexible body contact behaviors

Default Detection Method is:
-At Gauss Points for surface contact
−At Node Points Normal to Target for edge contact
Penetration Tolerance : Limit of maximum allowable penetration in the normal direction for penalty based formulation. Default is 10% of underlying element depth.
Elastic Slip Tolerance : Limit of max allowable “elastic slip” (parallel to frictional contact
− Default is 1% of average contact length in pair

Normal Stiffness is actually a factor (known as FKN) on the code calculated stiffness explained earlier.
─FKN=10.0 by default for Bonded and No Separation behaviors. FKN=1.0 by default for all other behaviors.
─For bending dominated situations, if convergence difficulties are encountered, a smaller value (FKN = 0.01 or 0.1) may be
─ Only applies to penalty based formulations (Pure Penalty or Augmented Lagrange)
Normal Stiffness is updated at each iteration by default
─ Based on the current mean stress of the underlying elements and the allowable
penetration
─ If bisections occur in the beginning of the analysis, the normal contact stiffness will be reduced by a factor of 0.2 for each bisection. The tangential contact stiffness will be updated at each iteration based on the current contact pressure, coefficient of friction (MU), and allowable slip (SLTO).